The role of electrodeionization (EDI) in water treatment
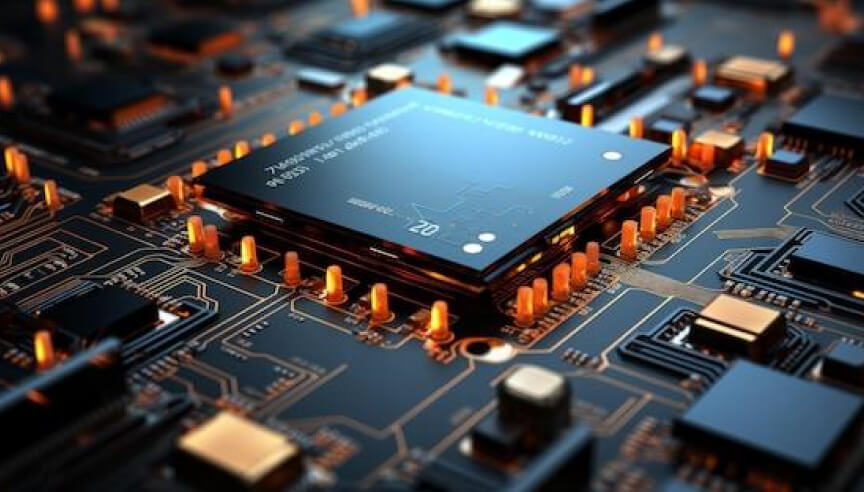
Electrodeionization (EDI) has emerged as a game-changing solution in this field, offering unmatched capabilities in producing the ultra-pure water required for semiconductor fabrication and other critical processes. In this article, we explore how EDI has become an indispensable tool in the realm of microelectronics manufacturing.
Revolutionizing Microelectronics Manufacturing: The Crucial Role of Electrodeionization (EDI)
In the fast-paced world of microelectronics manufacturing, where precision and purity are paramount, technologies that guarantee ultra-high purity water play a crucial role. Electrodeionization (EDI) has emerged as a game-changing solution in this field, offering unmatched capabilities in producing the ultra-pure water required for semiconductor fabrication and other critical processes. In this article, we explore how EDI has become an indispensable tool in the realm of microelectronics manufacturing.
The Demands of Microelectronics Manufacturing:
Microelectronics, including the production of semiconductors and integrated circuits, demands an exceptionally clean environment. Even trace impurities in water used during manufacturing processes can lead to defects, reduced yield, and compromised performance in the final products. To meet these stringent requirements, the industry relies on advanced water purification methods, with EDI at the forefront of this technological evolution.
How EDI Works in Microelectronics Manufacturing:
- Ultra-Pure Water Production: The EDI process involves the removal of ions and impurities from water through a combination of ion exchange resins and an applied electric field. This results in ultra-pure water, free from the contaminants that could compromise the delicate structures and materials used in microelectronics.
- Continuous Operation: One of the standout features of EDI is its ability to operate continuously. This is particularly advantageous in microelectronics manufacturing, where interruptions can lead to production delays and increased costs. EDI systems ensure a constant and reliable supply of ultra-pure water without the need for regeneration cycles.
- Elimination of Chemicals: Unlike some traditional water purification methods that rely on chemical regenerants, EDI minimizes the use of chemicals. This is a significant benefit for microelectronics manufacturers aiming to reduce the environmental impact of their processes while maintaining the highest purity standards.
- Consistent High Purity: The predictability and consistency of EDI systems make them ideal for microelectronics manufacturing. The technology achieves and maintains extremely high levels of water purity, crucial for ensuring the reliability and performance of electronic components.
Applications in Microelectronics:
- Semiconductor Fabrication: In the production of semiconductors, EDI is used to generate ultra-pure water for various critical processes, including wafer cleaning, photoresist development, and chemical mechanical planarization (CMP).
- Integrated Circuit Manufacturing: The intricate structures of integrated circuits demand water of the highest purity. EDI systems contribute to the production of pure water for etching, deposition, and rinsing steps in IC manufacturing.
- Clean Room Operations: EDI is instrumental in providing ultra-pure water for clean room operations, where even the slightest contamination can lead to defects in microelectronic devices.
Conclusion:
As microelectronics continue to advance in complexity and miniaturization, the demand for ultra-pure water in manufacturing processes becomes increasingly critical. Electrodeionization has not only met but exceeded these demands, establishing itself as an indispensable technology in the production of microelectronic components. With its continuous operation, reduced chemical usage, and consistently high purity levels, EDI has revolutionized the way the microelectronics industry approaches water purification, contributing to the production of high-performance and reliable electronic devices.