Recent Posts
Guide for selecting a pump
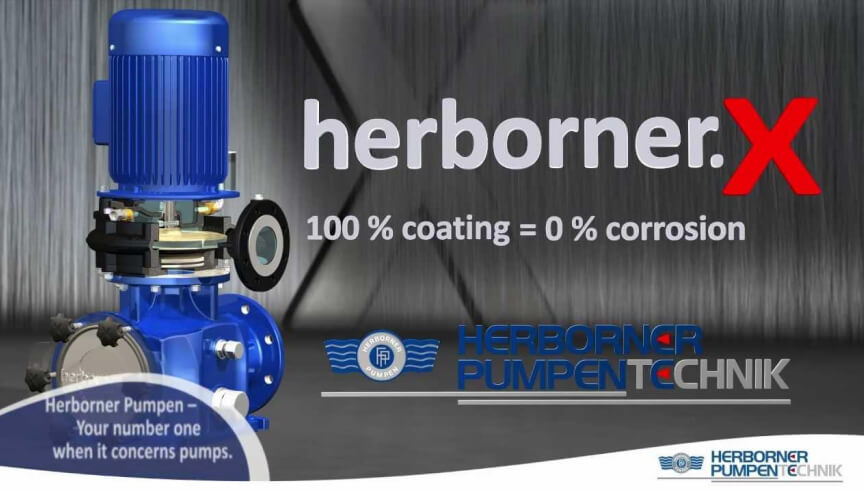
Selecting a pump based on performance involves evaluating key factors like flow rate, pressure, and efficiency. High-performance pumps handle larger volumes or higher pressures, ideal for industrial systems or large-scale water transfer. On the other hand, low-performance pumps suit smaller, controlled environments where precision matters more than power. Understanding your performance needs ensures you avoid oversizing or undersizing, optimizing energy consumption and longevity.
Pumps by Application
Pumps serve diverse industries, from water treatment to agriculture and chemical processing. Each application demands specific capabilities — irrigation systems need consistent, high-volume output, while chemical handling pumps must resist corrosion. Fire suppression systems require rapid response and reliable pressure, contrasting with gentle circulation pumps in heating systems. Matching the pump to the application ensures safe, effective, and long-lasting operation.
Pumps by Material and Internal Coating
Materials define a pump’s durability and resistance to wear, corrosion, or chemical attack. Stainless steel resists rust and handles aggressive chemicals, while cast iron withstands abrasive slurries. For added protection, internal coatings like epoxy or rubber lining shield components from corrosive or abrasive media. Careful material selection ensures longevity and minimizes maintenance, particularly in harsh environments.
Pumps by Type of Pumped Medium
The medium being pumped shapes pump design and materials. Water pumps handle clean, clear water efficiently, while slurry pumps tackle dense, abrasive mixtures. Chemical pumps resist aggressive fluids, and food-grade pumps ensure sanitary handling of consumables. Understanding the medium’s viscosity, temperature, and chemical properties ensures smooth operation and prevents damage or contamination.
Pumps by Type of Motor
Motors drive the pump, and their type affects efficiency and control. Electric motors are common for steady, reliable power, while diesel engines offer flexibility for remote sites. Hydraulic and pneumatic motors power specialized setups where electric power isn’t practical. Variable-speed motors provide energy savings by adjusting output to match real-time demand, improving overall system efficiency.
Pumps with Additional Functions and Equipment
Modern pumps integrate advanced features for enhanced performance and reliability. Built-in filters trap debris, protecting internal components and reducing maintenance. Double mechanical seals prevent leaks, essential for hazardous or high-pressure fluids. Anti-corrosion coatings extend lifespan in challenging environments, while fiber-cutting devices prevent clogging in wastewater or fibrous media. These additional features help tailor a pump to specific needs, improving safety, efficiency, and operational resilience.