Recent Posts
Water Treatment in Energy Generation
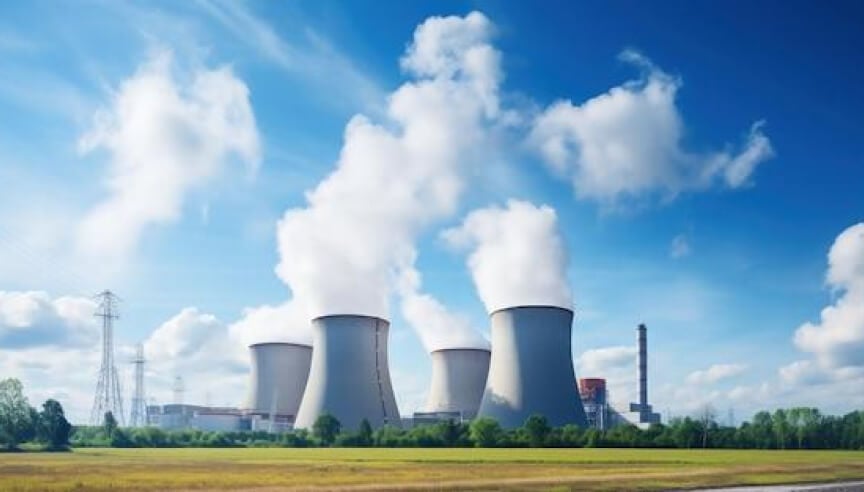
Water Treatment in Energy Production
Water is essential in energy production, whether for cooling, steam generation, or boiler feedwater. Ensuring the purity of water used in these processes is critical to maintaining system efficiency, preventing damage to equipment, and meeting environmental regulations. Various methods of water treatment, including filtration, deionization, and disinfection, are employed to meet the high standards required in energy production. This article explores the key water treatment techniques used in the industry.
1. Filtration: Mesh and Micro Sand Filters
Effective filtration is the first line of defense in water treatment for energy production. It removes particulate matter that can cause fouling, scaling, and corrosion in critical components such as boilers, turbines, and cooling systems.
- Mesh Filters:
Mesh filtration involves the use of fine screens made from metal or synthetic materials that trap particles as water passes through. Mesh filters are highly effective at capturing larger debris and can be used as a pre-filtration stage in conjunction with finer filtration systems. They are durable, easy to maintain, and ideal for continuous operations in high-flow environments such as power plants. - Micro Sand Filters:
These filters are highly efficient in removing smaller particles down to the micrometer scale. Micro sand filters work by passing water through layers of fine sand, which trap suspended solids. These filters can handle large volumes of water and are often used in cooling systems and feedwater treatment for boilers. The advantage of micro sand filtration is its high throughput and ability to capture fine particulates, improving water clarity and reducing the burden on downstream processes like ion exchange or membrane filtration.
2. Continuous Electrodeionization (CEDI)
Continuous Electrodeionization (CEDI) is a process that removes ionized and ionizable species from water using a combination of ion-exchange resins and electricity. CEDI is widely used in the energy sector to produce ultrapure water for applications such as high-pressure steam generation in power plants.
- How It Works:
In CEDI, water flows through a stack of ion-exchange membranes and resin beds. An electric field drives the separation of cations and anions, which are removed from the water stream and sent to a concentrate stream. This process continuously regenerates the resins without the need for chemicals, making it a sustainable and cost-effective solution. - Benefits in Energy Production:
The high purity water produced by CEDI is essential in preventing scaling, corrosion, and fouling in boilers and turbines. Since it operates without the need for chemical regeneration, CEDI reduces the risk of introducing contaminants and minimizes downtime. Its continuous operation makes it highly suited for large-scale energy production facilities that require consistent water quality.
3. Chemical and Chemical-Free Water Disinfection
Disinfection is a critical step in water treatment for energy production to prevent biofouling and maintain system integrity. Both chemical and chemical-free disinfection methods are used to control microbial growth, depending on the system design and regulatory requirements.
- Chemical Disinfection:
This involves the use of chemical agents such as chlorine, sodium hypochlorite, and chlorine dioxide to kill bacteria, viruses, and algae in cooling towers, boilers, and other systems. Chemical disinfection is highly effective, especially in systems with heavy microbial loads. However, chemical dosing must be carefully controlled to prevent the formation of harmful byproducts and avoid corrosion of system components. - Chemical-Free Disinfection:
In recent years, there has been a growing interest in chemical-free disinfection technologies such as ultraviolet (UV) light and ozonation. These methods are effective at inactivating microorganisms without introducing potentially harmful chemicals into the water system.- UV Disinfection:
UV systems use ultraviolet light to inactivate bacteria, viruses, and other microorganisms by disrupting their DNA. UV disinfection is a physical process, meaning no chemicals are added to the water. This makes it an excellent option for facilities seeking to reduce their chemical footprint while maintaining high levels of microbial control. - Ozonation:
Ozone is a powerful oxidant that is generated on-site using oxygen or ambient air. Ozone effectively eliminates microorganisms and breaks down organic contaminants in cooling water and feedwater systems. Since ozone decomposes into oxygen after disinfection, it leaves no residuals, making it an environmentally friendly option for water treatment in energy production.
- UV Disinfection:
Water treatment is a critical component in energy production, where high purity and reliability are essential. Filtration using mesh or micro sand filters provides the first level of protection by removing particulate matter, while continuous electrodeionization (CEDI) ensures the removal of dissolved ions to produce ultrapure water for steam generation and cooling systems. Disinfection, whether chemical or chemical-free, is necessary to control microbial growth and prevent fouling and corrosion. By combining these methods, energy facilities can maintain efficient, safe, and sustainable operations, reducing downtime and protecting valuable equipment.