Recent Posts
Water Purification Equipment in a Bottled Water Plant
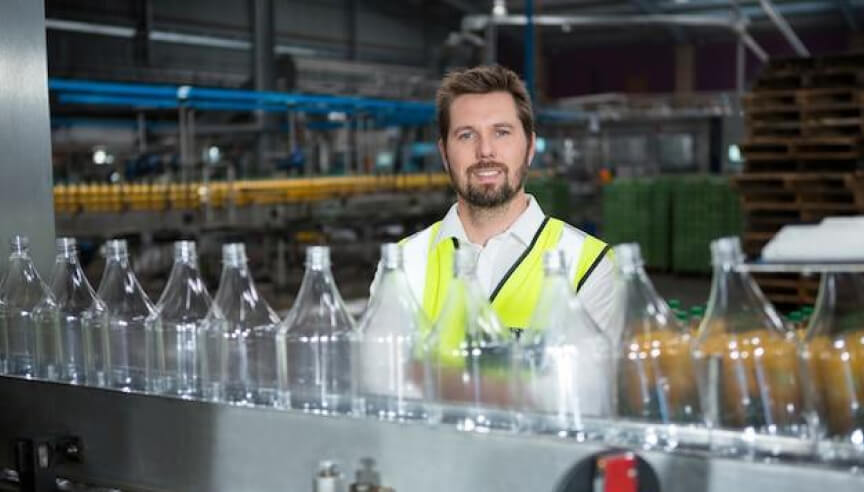
The Use of Water Purification Equipment in a Bottled Water Plant: A Comprehensive Guide to Filtration and Disinfection
Pre-Filtration of the Water Source
The foundation of producing premium bottled water lies in the careful treatment of the raw water source, starting with pre-filtration. This initial step is pivotal in ensuring the longevity of downstream systems and maintaining water clarity. An aluminosilicate-filled multimedia filter serves as an effective first barrier, targeting and removing larger suspended particles. This filter media excels in reducing turbidity and achieving filtration precision down to 1 micron. By preventing blockages in later stages, this method significantly enhances the overall efficiency and durability of the system, minimizing maintenance and operational interruptions. Moreover, effective pre-filtration helps safeguard sensitive membranes used in subsequent purification steps, promoting a seamless, high-performance water treatment process.
AQUAANALYTIC suggests using a combination of Mesh Filters and Multimedia Filters with AFM Activated Filter Media for sustainable results in pre-filtration. This will save Ultrafiltration and Reverse Osmosis membranes.
Ultrafiltration and Reverse Osmosis
Building on the groundwork laid by pre-filtration, ultrafiltration acts as an additional checkpoint. This advanced membrane technology functions at a molecular level, capturing microscopic contaminants, including bacteria, viruses, and fine particulates that might bypass earlier filters. It ensures that only the cleanest water advances to the reverse osmosis (RO) stage — the cornerstone of modern bottled water purification.
Reverse osmosis utilizes a high-pressure system to force water molecules through a semi-permeable membrane, which effectively screens out dissolved salts, organic compounds, and other pollutants. The result is water of extraordinary purity, free from unwanted flavors, odors, and chemical traces. RO technology is instrumental in bottled water production, especially for brands that prioritize clean, refreshing taste and adherence to stringent quality standards. Furthermore, the process significantly reduces total dissolved solids (TDS), ensuring consistency across every batch of bottled water.
The complete UF+RO plant from AQUAANALYTIC is fully automated and mounted on a plug and play mounting frame.
Ultraviolet Disinfection
Even after intensive filtration, an extra layer of microbial protection is necessary to ensure the highest safety standards. Ultraviolet (UV) disinfection steps in to deliver this safeguard. Emitting UV light at a precise wavelength, this method penetrates the cell walls of microorganisms, disrupting their DNA and neutralizing their ability to reproduce. This approach is highly effective against bacteria, viruses, and other pathogens, ensuring the final water product remains microbiologically safe without the use of chemicals. Unlike traditional disinfectants, UV treatment preserves the water’s natural taste and composition, making it an ideal choice for bottled water applications.
Ultraviolet systems that we offer are qualitatively different from analogues and are ideal for bottled water production plants. High-quality stainless steel for food production and systems of control over the operation of the installation guarantee quality results of the UV disinfection process and durability of the equipment.
Mineral Dosing for Water Variety
The purity achieved through reverse osmosis, while essential, also strips water of beneficial minerals that contribute to taste and nutritional value. To accommodate diverse consumer preferences, many bottled water plants incorporate a mineral dosing phase. This controlled reintroduction of essential minerals — such as calcium, magnesium, and potassium — allows manufacturers to create various product lines, from crisp, neutral-tasting water to mineral-enriched selections designed to support hydration and wellness. This process ensures consistency in flavor and composition, helping brands maintain a distinctive taste profile that meets market demands.
Stainless Steel Storage Tank
Once the water reaches its purified and mineral-enhanced state, it’s held in a stainless steel storage tank. Stainless steel is the preferred material due to its corrosion resistance and non-reactive properties, ensuring that the water remains untainted by external influences. The smooth, non-porous surface of stainless steel supports stringent hygiene standards by preventing bacterial buildup and simplifying cleaning and sterilization procedures. Additionally, the material’s durability ensures longevity, making it a cost-effective investment for high-capacity bottled water operations.
Ozone Treatment and Controlled Dosage
Ozone treatment stands as a final and crucial line of defense before the water is bottled. Ozone, a powerful oxidizing agent composed of three oxygen atoms, rapidly breaks down and neutralizes any remaining bacteria, viruses, or organic compounds. Unlike chlorine, ozone leaves no residual by-products or unwanted tastes, ensuring the water’s flavor remains crisp and refreshing.
Controlled ozone dosing is vital to this process. Over-oxidation can compromise the water’s taste and alter its chemical balance, while under-dosing may leave the product vulnerable to contamination. Precision in ozone application guarantees thorough disinfection without affecting sensory qualities. Additionally, ozone permeates the bottling system itself — including the filling lines and containers — ensuring that the entire packaging setup remains sterile and free from microbial threats.
Ozonators are an integral part of water production. We offer complete and complete Ozone Generators both for new production and for integration into existing plants.
Filling and Packaging
The final leg of the journey involves transferring the pristine, purified water into bottles. Modern filling machines operate in highly controlled, sterile environments, minimizing human interaction to prevent contamination. To enhance safety further, bottles are typically rinsed with ozone-treated water before filling, ensuring they remain sterile until sealed.
The filling process must strike a balance between speed and accuracy. High-speed systems ensure production keeps pace with demand, while precision mechanisms guarantee consistent fill volumes. Once filled, bottles are securely capped, labeled, and prepared for packaging. Automated packaging systems streamline this final step, reducing handling and maintaining product integrity.
Conclusion
From source to shelf, bottled water production hinges on an intricate balance of advanced filtration, disinfection, and handling technologies. Each phase — from pre-filtration to ozone treatment and packaging — plays an indispensable role in ensuring consumers receive bottled water that is safe, refreshing, and of the highest quality. By combining innovative equipment with rigorous processes, bottled water plants meet and exceed health and taste expectations, delivering a consistently excellent product to the market. AQUAANALYTIC will take your business to a higher level with top-of-the-line equipment and engineering solutions.